-
Transformation or bacterial contamination of the generated product
Presence of microscopic irregularities that worsen washability -
Rust floating or corrosion on a part of the pipe
Disturbance or deterioration of the composition of the oxide film that protects the inside of the pipe -
Red stains (rouge) appear in the tank, affecting the product
Change in quality or corrosion over time due to residue from processing -
High purity gas is contaminated with metal ions
Ions are generated due to insufficient surface treatment inside the piping
Metal surfaces in process piping are constantly exposed to stress and face the following problems
Semiconductor Manufacturing Industry
Unwanted Ion Contamination Worsens Yield
The trend toward higher performance semiconductor chips continues unabated. As a result, circuits are becoming finer and finer, and the difficulty of manufacturing is only increasing. At the same time, yield deterioration is unacceptable.
In semiconductor manufacturing, high-purity gases are used for inert gases and material gases. A small amount of metal ion contamination in these gases can have a significant impact on the performance and productivity of semiconductor chips.
Preventing contamination due to metal ion elution is an important issue in tanks and piping such as supply lines and filling lines for high-purity gases that require PPT-class purity.

Key point
In order to eliminate potential problems caused by insufficient thickness of the passive film, slight disturbance of the metal composition, and residual oxides and cleaning agents, it is recommended to strengthen the passive film after electropolishing.
Pharmaceutical manufacturing
Quality change due to rouge generation
In pharmaceutical and food manufacturing, rouge is a problem, especially in sanitary pipe lines that use pure water systems. Even in stainless steel pipes that have been passivated, red* rust gradually arises inside the pipes, and this is called rouge.
It is common in places where the surface of the piping is deteriorated or corroded, or in welded areas, and it occurs in places that are prone to extremely high temperatures, making it a major issue for validation.
*Depending on its composition, rouge has various colors such as red/orange, black/grey, and brown. Although some rouges are inert, they may become active after a certain period of time.

Key point
The cause of rouge lies in the effects of processing, such as residual buffing powder oil and sharp striations. Furthermore, if finish polishing and cleaning to remove these are insufficient, the cause of rouge will be internalized even if electropolishing is applied.
Food processing industry
Food contamination due to growth of germs
Carbohydrates, proteins, fats, and other substances from food adhere to the machine and become degenerated. Since these substances can get mixed into food and become a breeding ground for microorganisms, food machinery should have a “sanitary structure” that (1) prevents adhesion and accumulation of liquid, and (2) facilitates cleaning, sterilization, and disinfection.
However, there are areas that cannot be cleaned, especially welds in piping, due to inadequate matching accuracy, weld finish, post-weld polishing and surface treatment. It is said that incomplete cleaning often results in insufficient effectiveness of subsequent disinfection treatment. As a result, microorganisms and their toxins, which are biological hazards, will remain in the food, and the quality of the food product will be affected.

*HACCP (Hazard Analysis and Critical Control Point) is a system in which a food business operator identifies hazard factors (hazards) such as contamination by food poisoning bacteria and foreign matter, and then establishes a process that is particularly important for eliminating or reducing these hazards in all processes from the receipt of raw materials to the shipment of products. This is a hygiene management method to ensure the safety of products by controlling particularly important processes to eliminate or reduce such hazards in all processes from the receipt of raw materials to the shipment of products (from the website of the Ministry of Health, Labor and Welfare).
Key point
Pay attention to inappropriate selection of processing materials, average roughness outside the standard range, grinding with disordered grain size, neglect of fine cavities created by machining, partial welding, rough back waves, inappropriate internal angle welding, etc.
General and common
Shortening the service life of equipment due to pitting corrosion and crevice corrosion
Even with surface-treated stainless steel piping, care must be taken to avoid pitting corrosion and crevice corrosion, which can cause localized corrosion of the corrosion protection film on straight pipes and joints. In an environment where chloride ions are handled or come into contact with, the progression of corrosion varies greatly depending on the quality of metal processing and surface treatment, even for highly corrosion-resistant stainless steel.
Residual stress from welding and other processes can cause stress corrosion cracking and other problems that shorten the life of production equipment. Such surface degradation progressively affects the quality of the produced product even before it becomes seriously damaged.

Key point
Formation of a heterogeneous passive film, surface contamination due to insufficient pre-cleaning in advance. Oxides and electrolyte components remain on the metal surface even after finish cleaning.
If you think there might be a problem with the surface of the metal, please think of Nissho Astec’s surface treatment solution
-
Surface treatment of process piping and tanks is our specialty.
-
We can propose processing that maximizes the effect of surface treatment.
-
We stock stainless steel pipes with surface treatment (one of the best in Japan).
-
Our Vietnamese subsidiary is also capable of pharmaceutical class processing and electropolishing.
Surface treatment solutions provided by Nissho Astec
*The pictures are for illustrative purposes only and may differ from the actual product or service.
Click here to learn more about each menu of surface treatment.
Mechanical polishing – Buffing and vibratory polishing
Remove unevenness on the metal surface mechanically.
The unevenness on the metal surface is mechanically removed to create a flat surface. The finish of buffing depends on the particle size of the abrasive used, the characteristics of the machine, and the skill level of the craftsman.

Note
-
It is possible to make a mirror-like glossy surface in terms of shape. Compositionally, it is not stable due to the effects of processing heat.
-
Shape-wise: In buffing, the unevenness of the surface is mechanically crushed. Therefore, even though the surface may look beautiful and shiny on a visual level, on a microscopic level, there are voids and valleys of traces. Metal powder, abrasives, oil, etc. are left behind in the gaps.
-
Composition: The surface layer of the metal is in an active (easily changeable) state due to changes in the metal’s structure and crystal structure caused by the heat of welding and buffing.
Key point
High grade precision polishing of long pipes (VI NA ASTEC) with electropolishing and other post-processing in mind. The longitudinal striations left on the sanitary pipe are no longer noticeable, resulting in a high-grade finish inside the pipe. The effect of electropolishing is further enhanced and purification is increased.
More information
Read more about Cross Polishing + Electropolishing Finishing
Read more about Buffing of pure titanium and titanium alloy castings
Electrolytic Polishing (EP)
Electrolytic polishing dissolves microscopic unevenness of metal surfaces to flatten and homogenize them.
Electrolytic action dissolves the convexity of the metal surface and flattens the shape of the metal surface. In the process, a passivation film and a chromium-rich layer by chromium concentration are formed on the surface (1 to 3 nm). This contributes to a significant improvement in corrosion resistance.
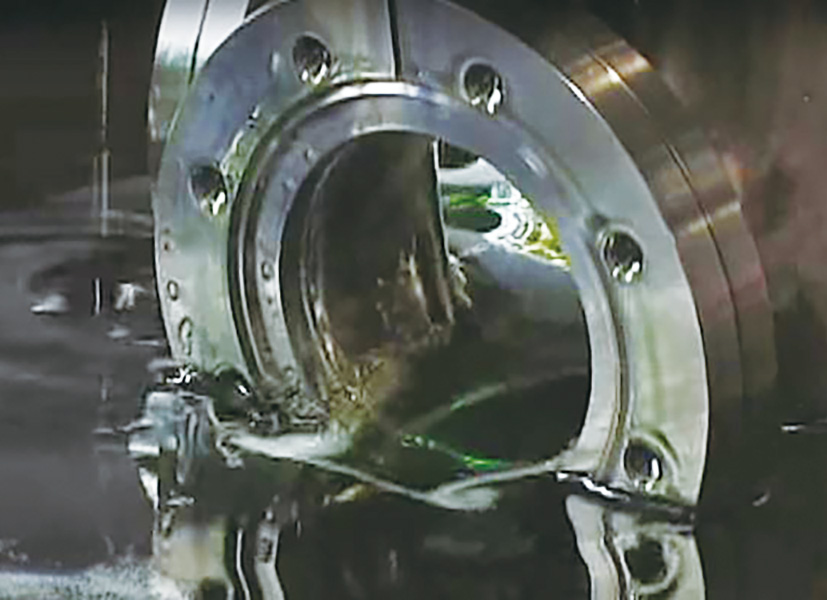
Note
-
Dissolution by electropolishing is a microscopic electrolytic reaction on the metal surface, and cannot eliminate large striations. To increase the flatness, it is necessary to perform institutional high mechanical polishing beforehand.
-
Contaminants on the surface can be removed to some extent during the electrolytic reaction. However, depending on the metal surface and the contaminants, electropolishing may not be sufficient for the purpose of contaminant removal.
-
Composition: The heat from welding and buffing processes changes the structure and crystalline structure of the metal, leaving it in an active (changeable) state.
Key point
If you do not want your product to be contaminated by metal elution, Gold EP (GEP)/Gold EP White (GEPW) described below with enhanced passive film is strongly recommended.
More Information
Read more about electrolytic polishing
Electrolytic polishing of aluminum and titanium (VINA ASTEC)
Gold EP (GEP) / Gold EP White (GEPW)
Surface protection and suppression of metal elution through the formation of a thick, homogeneous oxide film.
The passive film formed by electropolishing is flat and homogeneous, but its thickness is not thick (1~3nm), and it may have potential crystal disorder locally. Gold EP(GEP)/Gold EP White(GEPW) are heat-treated for a certain period of time after EP to grow a thick oxide film on the surface.
GEP/GEPW is used for high-purity gas lines, etc., because the elution of metal dissolved ions is suppressed to an extremely low level. It is also clean because the slight amount of organic matter that remains on the metal surface is reduced during the heat treatment process.
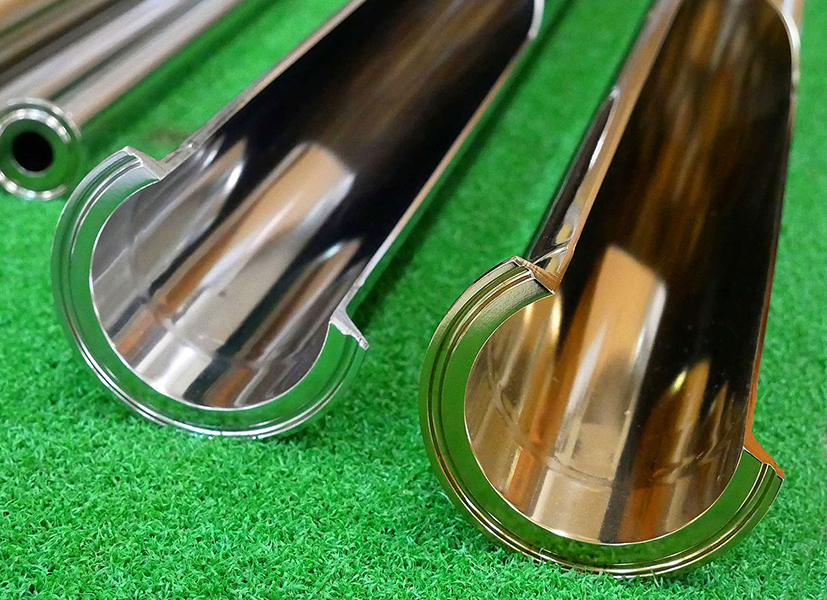
Key point
-
GEP causes chromium oxide and iron oxide films to grow on the surface after EP, and their thickness is 10 times that of the drug during EP.
-
GEPW is a chemical treatment of GEP to dissolve the iron oxide film on the surface layer. The chromium oxide film is about three times that of EP.
More information
Degreasing cleaning – Alkaline degreasing cleaning (immersion method)
Remove dirt from the metal surface, focusing on adhered oil.
A variety of contaminants (metal powder, machine oil, buffing powder, metal smut, etc.) adhere to the surface of metal after processing. In alkaline degreasing cleaning, these contaminants are dissolved, lifted, and removed by the saponifying action of alkaline chemicals and surfactants.
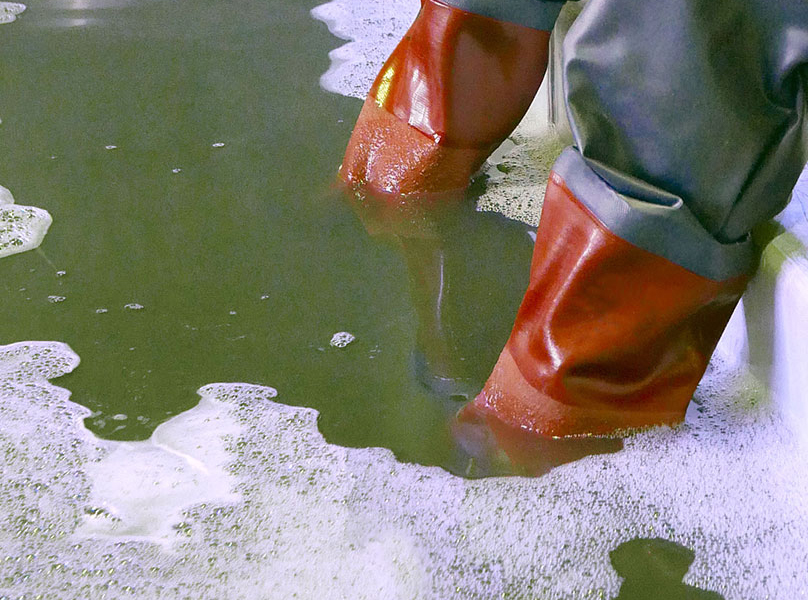
Note
-
With immersion in alkaline chemicals, it is impossible for the chemicals to penetrate and come into contact with all the uneven parts of the metal surface, which limits the removal of stains.
-
Even if passivation is performed after alkali degreasing, it is difficult to eliminate all structural and compositional inhomogeneities caused by buffing and welding. To create a better surface, it is desirable to dissolve the convexity and create a homogeneous passive film by electropolishing.
More information
Post-processing for electropolishing – Alkaline degreasing and weak acid cleaning
Removes mainly oxides and other substances in the electrolytic treatment to prepare the surface.
Removes oxides dissolved by the electropolishing process, electrolytic solution, and other adhering substances. The degreasing effect of alkali treatment varies depending on heating and concentration. Alkali treatment dissolves metal surfaces and removes stains that have penetrated the surface.
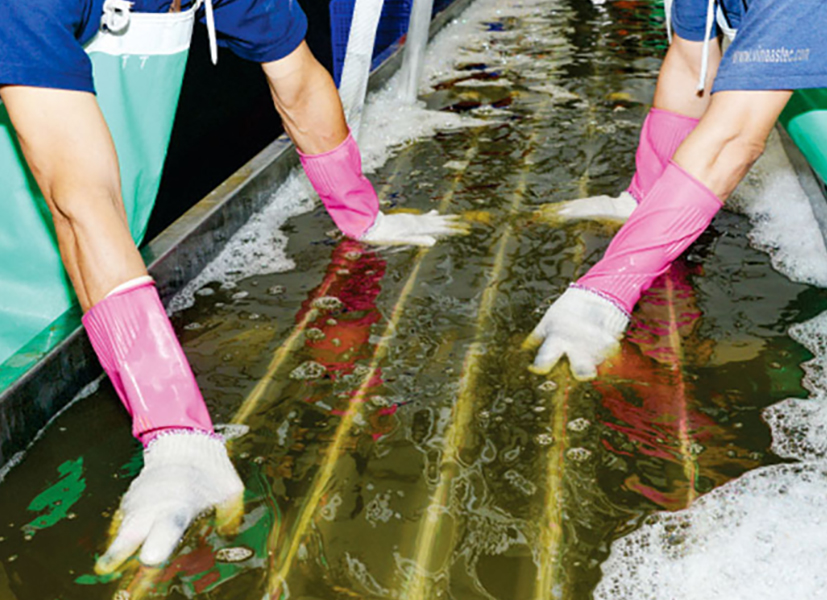
Note
-
Since alkaline treatment involves dissolution of the metal surface, post-treatment includes neutralization with weak acid and regeneration of the passive film.
More information
Pickling / Rust removal
Removes scale, dirt, and rust from welding and other processes.
Pickling is used to remove bead scale and oxide film scale after welding. It also removes fine burrs, oil and other contaminants. Pickling also removes the passive film of stainless steel, which is immediately regenerated after pickling.

Note
-
Since sulfuric acid and hydrochloric acid are used for pickling, care must be taken in their storage, handling, disposal of residual liquid and cleaning solution, and toxic gases.
-
When pickling is used as a finish, the metal surface becomes pearly and not smooth.
More information
Examples of rust removal from steel products (VINAASTEC)
*We do not provide rust removal services for iron products in Japan.
Precision cleaning with ultrapure water / Regular cleaning
Clean cleaning required after electropolishing or chemical cleaning.
In surface treatment processes such as electropolishing, GEP, GEPW, etc., in addition to immersion cleaning in alkali or acid, high-pressure cleaning with ultrapure water*1 is performed*2. Since ultrapure water does not contain various ions, it can remove particles without contamination by them.

*1Ultrapure water: Ultrapure water manufacturer’s guaranteed value: 17.5 MΩ-cm (guaranteed outlet value)
*2High-pressure washing: 6 MPa/about 60°C
Key point
-
Water easily dissolves things, and tap water contains ions such as calcium, magnesium, and chloride. In order to prevent these unwanted ions from contaminating products during cleaning, products that require a high level of cleanability are cleaned with ultrapure water.
Pure steam cleaning (PS)
Ultra-clean cleaning of inner surfaces of tanks and containers using high-temperature steam.
Pure steam (PS) cleaning involves filling a tank or container with hot steam from pure water (we use RO water) for a certain period of time to lift off dirt. The hot steam reaches even the tiniest details that liquid water cannot penetrate due to surface tension, and is expected to remove dirt and bacteria.
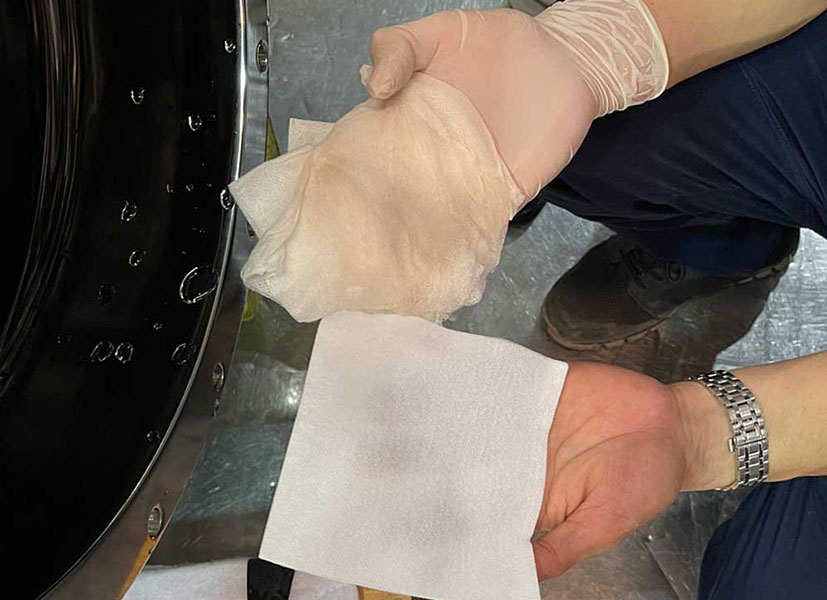
Key point
-
Pure steam cleaning is handled by our local subsidiary in Vietnam – VINA ASTEC.
More information
Clean air drying / Nitrogen blowing
Drying or blowing off residual moisture and fine foreign matter
Blow with clean air or nitrogen gas. Air is cleaned by hollow fiber filter (0.01μm filtration). In a thermal drying oven (with a 0.3μm HEPA filter), drying is performed at a drying temperature of 60°C for at least 30 minutes.
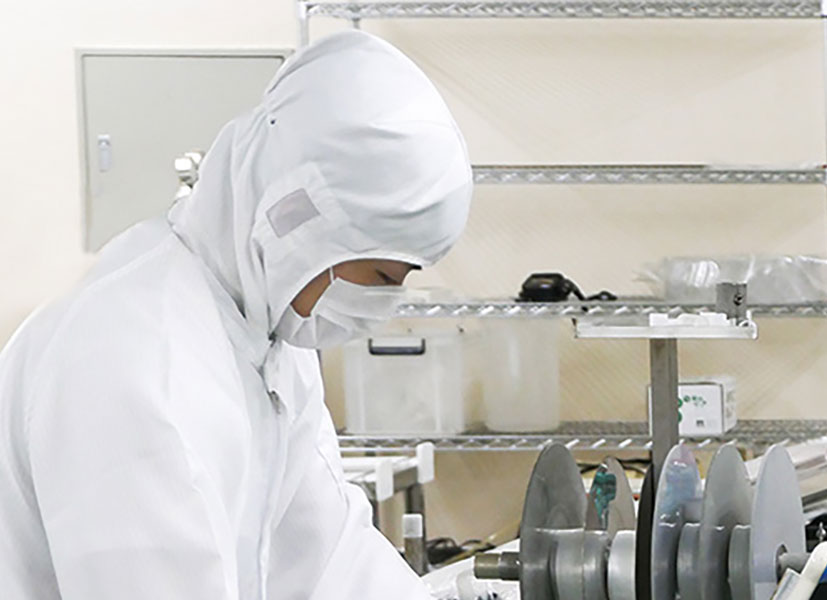
Key point
-
Final inspection and packaging are done in a clean room (JIS B9920 Class 6) where particles are removed.
-
Nitrogen blowing is used when static electricity generation and oxidation are to be prevented.
More information